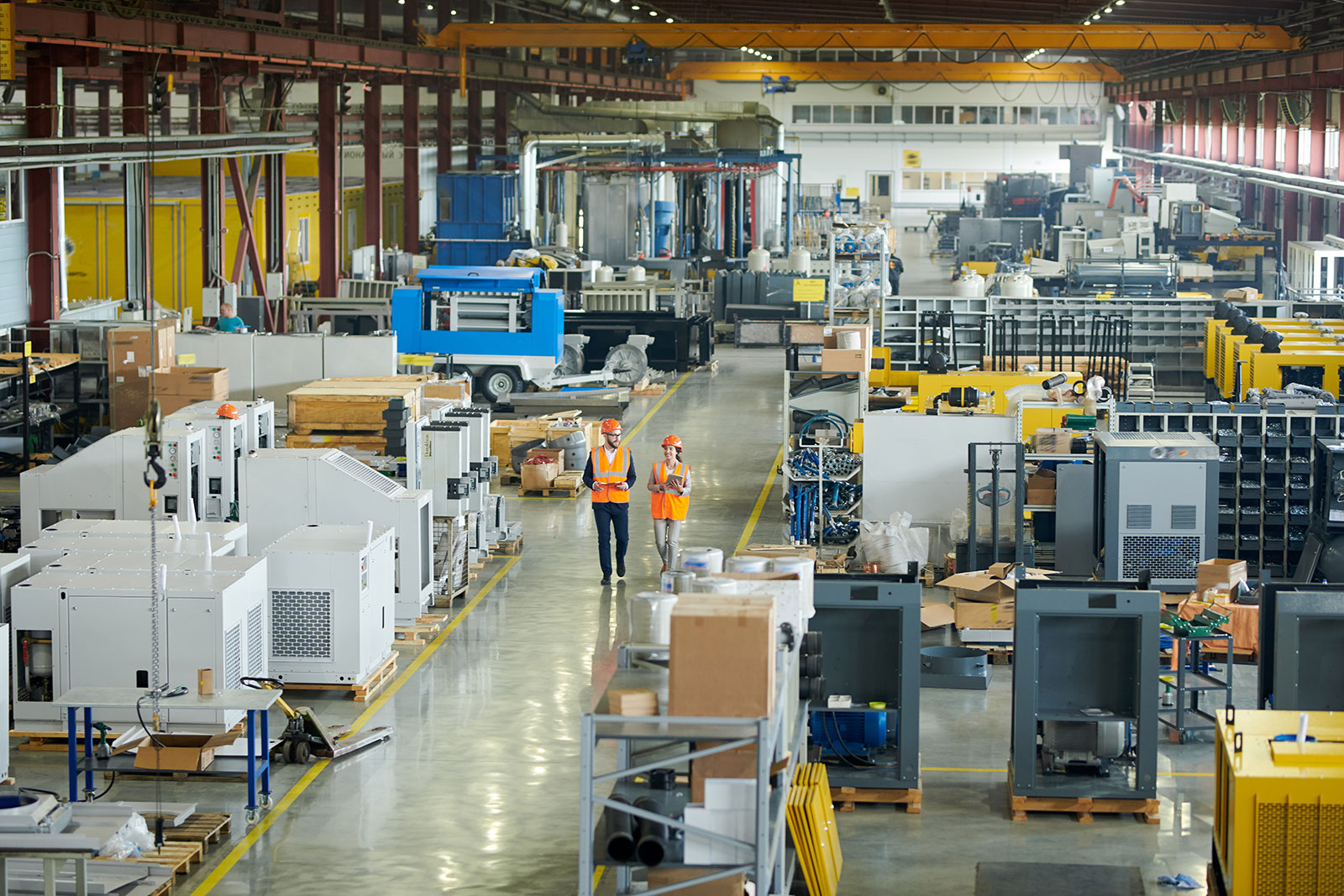
Prawidłowe podłączenie instalacji po relokacji maszyn przemysłowych
Każda relokacja maszyn przemysłowych to wyzwanie równe postawieniu pierwszych kroków na nowej drodze technologicznej.
Znaczenie mają tu nie tylko aspekty techniczne, takie jak elektryka czy hydraulika, ale również odpowiednia dokumentacja i zapewnienie, że po relokacji produkcja wróci do swojego rytmu bez zbędnych przestojów. Przyjrzymy się, jak złożony i wymagający jest to proces, który, gdy jest wykonany profesjonalnie, gwarantuje dalszy rozwój i efektywność przedsiębiorstwa.
Planowanie i przygotowanie do relokacji maszyn przemysłowych
Efektywnie przeprowadzona relokacja maszyn przemysłowych wymaga szczegółowego planowania i przygotowania. Strategiczne podejście do tego procesu jest kluczowe dla zapewnienia bezpieczeństwa i minimalizacji przestojów produkcyjnych. Oto kilka istotnych kroków, które należy uwzględnić w planie:
- Analiza techniczna i dokumentacyjna maszyn – zrozumienie wymagań technicznych i specyfikacji maszyn jest niezbędne do zaplanowania odpowiednich zasobów i narzędzi.
- Wybór kompetentnego zespołu – doświadczeni specjaliści są w stanie przewidzieć potencjalne problemy i zapewnić efektywność całego procesu.
- Harmonogram prac – ustalenie realistycznego harmonogramu pozwala na koordynację działań i minimalizację czasu przestoju.
- Bezpieczeństwo – opracowanie planu bezpieczeństwa jest niezbędne do ochrony pracowników i sprzętu podczas relokacji.
- Komunikacja z zespołem – jasne wytyczne i stały przepływ informacji zapewniają sprawną współpracę i realizację projektu zgodnie z planem.
Wybór odpowiedniego zespołu do przeprowadzenia relokacji
Podjęcie decyzji o przeniesieniu maszyn przemysłowych to zadanie wymagające szczególnej uwagi i doświadczenia. Profesjonalny zespół zajmujący się relokacją masz przemysłowych powinien posiadać nie tylko odpowiednią wiedzę techniczną, ale również doświadczenie w zarządzaniu projektami oraz logistyce. Znaczenie ma tutaj zarówno znajomość specyfiki branży, jak i umiejętność szybkiego reagowania na nieprzewidziane sytuacje, które mogą pojawić się podczas przemieszczania ciężkiego sprzętu. Dlatego też, wybierając wykonawcę, należy zwrócić uwagę na jego dotychczasowe realizacje oraz referencje od poprzednich klientów, co pozwoli na ocenę kompetencji i wiarygodności firmy.
Przy wyborze odpowiedniego zespołu warto również zwrócić uwagę na aspekty związane z bezpieczeństwem pracy. Firma odpowiedzialna za relokację powinna przestrzegać obowiązujących norm i przepisów BHP, co jest gwarancją nie tylko ochrony zdrowia pracowników, ale także sprzętu i infrastruktury klienta. Ponadto, istotne jest, aby zespół posiadał ubezpieczenie od odpowiedzialności cywilnej, które zabezpieczy interesy wszystkich stron w przypadku ewentualnych szkód. Podsumowując, dokładna weryfikacja potencjalnych wykonawców jest kluczowa dla sukcesu całego przedsięwzięcia i powinna być przeprowadzona jeszcze przed rozpoczęciem właściwych działań relokacyjnych.
Bezpieczny demontaż i transport maszyn przemysłowych
Realizacja procesu demontażu i transportu maszyn przemysłowych wymaga szczegółowego planowania i przestrzegania odpowiednich procedur bezpieczeństwa. Zespół odpowiedzialny za przeniesienie powinien być wyposażony w niezbędne narzędzia i wiedzę techniczną, aby zapewnić ochronę zarówno sprzętu, jak i personelu. Należy pamiętać o:
- Zabezpieczeniu ruchomych części maszyn przed przemieszczaniem się.
- Oznakowaniu i zabezpieczeniu wszystkich połączeń elektrycznych i hydraulicznych.
- Użyciu odpowiednich środków transportowych dostosowanych do wagi i gabarytów maszyn.
Dokładne oznaczenie wszystkich elementów maszyny jest kluczowe dla późniejszego etapu ponownego montażu. Każdy element powinien być jasno oznaczony, co ułatwi jego identyfikację i zapobiegnie pomyłkom podczas relokacji maszyn. Ponadto, warto skorzystać z usług specjalistycznej firmy, która posiada doświadczenie w relokacji maszyn przemysłowych, co znacząco zwiększa szanse na bezproblemowy demontaż i transport.
Przed przystąpieniem do transportu, niezbędne jest dokładne przygotowanie miejsca docelowego. Obejmuje to weryfikację warunków technicznych, takich jak dostępność odpowiednich przyłączy elektrycznych i hydraulicznych, a także zapewnienie, że podłoga jest w stanie wytrzymać ciężar przenoszonej maszyny. Tylko w pełni przygotowane i zabezpieczone miejsce gwarantuje, że instalacja po relokacji będzie przebiegać sprawnie i bez zakłóceń.
Kluczowe aspekty podłączenia elektrycznego po relokacji
Podczas ponownego podłączania instalacji elektrycznej po relokacji maszyn przemysłowych, niezwykle istotne jest dokładne zaplanowanie całego procesu. Należy szczegółowo przeanalizować i odwzorować oryginalne schematy połączeń, aby zapewnić bezproblemowe i bezpieczne działanie urządzeń. Nieprawidłowe podłączenie może prowadzić do awarii maszyn, a w skrajnych przypadkach nawet do zagrożenia życia pracowników. Dlatego też, zaleca się skorzystanie z usług doświadczonych specjalistów, którzy posiadają odpowiednią wiedzę i narzędzia do wykonania tego zadania.
Staranne oznakowanie wszystkich elementów instalacji elektrycznej przed demontażem jest kluczowe dla późniejszego, prawidłowego podłączenia. Wszelkie nieścisłości mogą prowadzić do błędów, które będą trudne do zidentyfikowania po zakończeniu procesu relokacji. Należy również pamiętać o sprawdzeniu zgodności parametrów elektrycznych w nowej lokalizacji z wymaganiami maszyn, co jest niezbędne do ich prawidłowego funkcjonowania. W tym kontekście, nie można pominąć takich aspektów jak napięcie, częstotliwość prądu oraz dostępność odpowiednich zabezpieczeń.
Zastosowanie nowoczesnych narzędzi diagnostycznych może znacząco przyczynić się do skrócenia czasu potrzebnego na podłączenie instalacji elektrycznej oraz zwiększenia precyzji całego procesu. Użycie takich urządzeń pozwala na szybką weryfikację poprawności połączeń i identyfikację ewentualnych problemów. Jest to szczególnie ważne w przypadku skomplikowanych systemów, gdzie ręczne śledzenie każdego przewodu byłoby czasochłonne i podatne na błędy. Dlatego też, inwestycja w odpowiednie technologie może przynieść długoterminowe korzyści i zapewnić większą niezawodność działania przeniesionych maszyn.
Weryfikacja hydraulicznych i pneumatycznych systemów instalacyjnych
Po przeprowadzeniu relokacji maszyn przemysłowych, kluczowe jest staranne sprawdzenie wszystkich elementów hydraulicznych i pneumatycznych przed ich ponownym uruchomieniem. Należy dokładnie skontrolować, czy wszystkie połączenia są szczelne i czy nie doszło do uszkodzenia rur, węży czy złączek. Weryfikacja ta powinna obejmować:
- Testy ciśnieniowe układów, aby wykryć ewentualne nieszczelności.
- Inspekcję wizualną komponentów w poszukiwaniu uszkodzeń mechanicznych.
- Kontrolę zgodności zaktualizowanych schematów instalacyjnych.
Takie działania zapobiegają ryzyku awarii i przestojów, które mogą generować znaczne koszty dla przedsiębiorstwa.
Zarazem, niezwykle istotne jest zastosowanie odpowiednich narzędzi i technik podczas weryfikacji systemów. Użycie nieprawidłowych metod może prowadzić do błędnych wniosków i w konsekwencji do nieprawidłowego działania maszyn. Specjaliści odpowiedzialni za ten proces powinni być wyposażeni w:
- Manometry i czujniki ciśnienia do precyzyjnych pomiarów.
- Detektory ultradźwiękowe do wykrywania niewidocznych nieszczelności.
- Profesjonalne zestawy do czyszczenia i konserwacji elementów hydraulicznych i pneumatycznych.
Dzięki temu możliwe jest gwarantowanie bezpieczeństwa i niezawodności maszyn po ich relokacji i ponownym montażu.
Kalibracja i testowanie maszyn po ponownym podłączeniu
Należyte przeprowadzenie kalibracji i testowania maszyn po ich relokacji jest kluczowe dla zapewnienia ich prawidłowego działania. Proces ten powinien być przeprowadzony przez wykwalifikowany personel, który dokładnie zna specyfikację techniczną danego urządzenia. Kalibracja pozwala na dostosowanie maszyn do nowych warunków pracy, co jest niezbędne dla zachowania precyzji i efektywności produkcyjnej. Testowanie natomiast umożliwia weryfikację, czy wszystkie funkcje maszyny działają poprawnie po relokacji. Poniżej przedstawiamy kluczowe kroki, które należy podjąć:
- Weryfikacja dokumentacji technicznej – przed rozpoczęciem kalibracji należy sprawdzić, czy dysponujemy aktualnymi schematami i instrukcjami obsługi.
- Kontrola stanu technicznego – ocena wizualna oraz testy mechaniczne pozwalają na wykrycie ewentualnych uszkodzeń, które mogły wystąpić w trakcie transportu.
- Regulacja parametrów – dostosowanie ustawień maszyny do nowego miejsca pracy, z uwzględnieniem takich czynników jak temperatura, wilgotność czy poziom wibracji.
- Testy funkcjonalne – przeprowadzenie serii prób produkcyjnych, aby upewnić się, że maszyna pracuje zgodnie z oczekiwaniami.
- Analiza wyników – dokładne przeanalizowanie danych z testów i porównanie ich z parametrami nominalnymi.
Po zakończeniu procesu kalibracji i testowania, niezwykle ważne jest dokumentowanie wyników. Umożliwia to późniejszą weryfikację ustawień oraz szybką diagnostykę w przypadku wystąpienia problemów. Należy również pamiętać o przeszkoleniu personelu z obsługi zaktualizowanych maszyn. Wdrożenie tych procedur gwarantuje nie tylko bezpieczeństwo, ale także optymalizację procesów produkcyjnych i minimalizację ryzyka przestojów. Dzięki temu, inwestycja w profesjonalne podejście do kalibracji i testowania maszyn po relokacji szybko się zwraca, przyczyniając się do wzrostu efektywności całego przedsiębiorstwa.
Dokumentacja techniczna i protokoły z relokacji
Zarządzanie procesem relokacji maszyn przemysłowych wymaga szczegółowej dokumentacji technicznej. Dokumentacja ta powinna zawierać wszystkie istotne informacje dotyczące demontażu, transportu, montażu oraz ponownego uruchomienia maszyn. Jest to kluczowe dla zapewnienia ciągłości pracy i minimalizacji ryzyka wystąpienia awarii. Dokumentacja powinna być tworzona w oparciu o następujące kroki:
- Zgromadzenie oryginalnych schematów i instrukcji obsługi maszyn.
- Dokładne oznaczenie wszystkich elementów instalacji przed demontażem.
- Tworzenie szczegółowych protokołów z każdego etapu relokacji.
Protokoły z relokacji są niezbędne nie tylko dla potwierdzenia prawidłowości wykonanych prac, ale również dla ewentualnych przyszłych inspekcji czy audytów. Powinny one zawierać dokładny opis procesów oraz wszelkie zmiany, które zaszły w trakcie relokacji. Wśród najważniejszych elementów protokołu znajdują się:
- Dokładny opis stanu technicznego maszyn przed i po relokacji.
- Rejestracja wszelkich napotkanych problemów oraz sposobów ich rozwiązania.
- Weryfikacja zgodności ponownego montażu z dokumentacją techniczną.
Zachowanie ciągłości procesów produkcyjnych po relokacji wymaga starannego planowania i przestrzegania procedur. Dokumentacja techniczna i protokoły są podstawą do przeprowadzenia niezbędnych testów i uruchomienia maszyn w nowej lokalizacji. W tym kontekście, kluczowe jest:
- Przeprowadzenie testów funkcjonalnych w celu potwierdzenia prawidłowości działania maszyn.
- Analiza wyników i porównanie ich z parametrami określonymi w dokumentacji technicznej.
- Przygotowanie raportu końcowego, potwierdzającego gotowość maszyn do wznowienia produkcji.
Zapewnienie ciągłości produkcji po relokacji maszyn
Aby zminimalizować przestoje w produkcji po relokacji maszyn przemysłowych, niezbędne jest staranne zaplanowanie całego procesu. Kluczowe jest przestrzeganie checklisty, która powinna zawierać: weryfikację zgodności specyfikacji technicznych maszyn z nowym miejscem instalacji, ponowne przeprowadzenie testów bezpieczeństwa, a także dokładne sprawdzenie wszystkich połączeń elektrycznych i mechanicznych. Utrzymanie ciągłości produkcji wymaga również zabezpieczenia odpowiedniej infrastruktury – zarówno pod kątem dostaw energii, jak i sieci komunikacyjnych. Profesjonalne oznakowanie wszystkich elementów instalacji i przewodów może znacząco przyspieszyć proces ponownego uruchomienia maszyn oraz ułatwić przyszłe prace serwisowe.